Plastic injection moulding is a highly versatile process used by the majority of manufacturing companies. It offers a wide choice of moulding materials like silicon, glass, iron etc., enabling manufacturers to produce identical parts made from various materials. Read on to know about the core benefits of plastic injection moulding in the manufacturing industry, ways to purchase one and more.
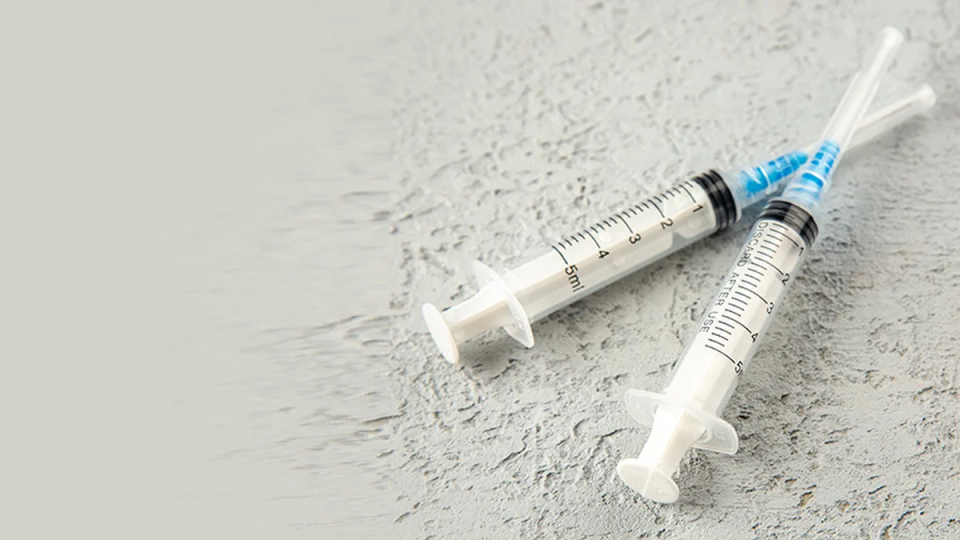
10 Major Benefits of Plastic Injection Moulding Equipment
The widespread usage of injection moulding happens due to its numerous advantages over other industrial processes. Here are some of the ten major benefits of using plastic injection moulding equipment:
1. High Accuracy and Precision
Through injection moulding, factories can create precise and accurate items in large volumes. The entire process is conducted in a controlled environment to produce identical and uniform items and maintain consistency in quality.
Furthermore, the moulds which are used to produce items can also be customised as per requirements. It enables manufacturers to make even more precise and accurate items such as incorporating undercuts, inserts, threads, etc.
2. Materials Choice
Injection moulding offers a wide range of material options for manufacturing various material products. The materials can be various types of plastic such as Polyethylene Terephthalate, Polypropylene, Polymethyl Methacrylate Polyvinyl Chloride, etc. Other than plastic, moulding material can be silicon, glass, iron, etc.
This level of versatility is useful for manufacturers as they can switch materials if any set of items demands stiffness, high strength and rigidity. Also, to produce heat-resistant products, the manufacturer can simply switch to epoxy or phenolic which is a thermostat material.
3. Cost-effective
Plastic injection moulding is one of the cost-effective techniques used in the manufacturing industry. Using this method, the cost per unit decreases with the increase in the production volume. By availing a Machinery Loan online, companies can leverage the low production costs to increase their capacities and fulfil bulk orders.
Moreover, injection moulding can also be automated which can save the cost of labour to a large extent. It is also capable of producing high-volume precise items which reduces the cost of post-manufacturing processes such as trimming and sanding.
4. Low Wastage
The scrap rate of materials in the injection moulding process is minimal, as much of the scrap produced can be recycled. Reusing scrap not only reduces wastage but also reduces the overall cost of production, resulting in higher profits.
Plastic mould designs are created in such a way so that the molten raw materials are distributed evenly leaving no air bubbles or any other defects in the item. This ensures that the items hardware produces are accurate and of the highest quality.
5. Design Flexibility
When using injection moulding, manufacturers get the flexibility of manufacturing items of almost any design as per the requirement. It allows the freedom to create and customise mould designs and produce complex and accurate geometries. It enables manufacturers to incorporate undercuts, inserts, threads, etc., to create customised parts for customers.
6. Consistent Results
The entire process of manufacturing is conducted in an automated and controlled environment to maintain preciseness, consistency and uniformity in the item outputs. This control environment is strictly maintained in each and every stage of production in injection moulding, including the stages of clamping, injecting, cooling, and ejecting. It helps in maintaining uniformity and minimises quality variations.
7. Reduced Labour Costs
Injection moulding machines are highly automated and reduce the labour-oriented costs of the manufacturing process. Once the machinery is set up and proper inputs are provided, the process can continue without any human intervention till the final outputs are discharged from the machine. This reduces the overall labour cost of manufacturing.
8. Minimal Post-processing Requirements
The final outputs produced are usually uniform, accurate and of the highest quality with minimal variation. This eliminates extensive post-processing processes such as sanding and polishing to give a precise dimension to the product.
9. Environmental Benefits
Injection moulding is considered one of the most eco-friendly manufacturing techniques, as the material scrap generated in the manufacturing process is minimal. This results in low usage of raw materials in the manufacturing process making it more cost effective. Moreover, this method also consumes less energy compared to other manufacturing techniques available in the market.
10. Faster Cycle
The manufacturing process in injection moulding involves four stages such as clamping, injection, cooling and ejection. The integration of automation helps in the completion of these four stages in a very short span of time. This enables manufacturers to produce high-volume output without compromising on quality and accuracy.
How to Purchase Plastic Injection Moulding Equipment for Your Factory?
Thorough research is required before purchasing plastic injection moulding equipment for your factory. Here are some of the steps to consider:
1. Understand the Plastic Components You Plan to Mould
It is crucial to know the details of the plastic item you are willing to manufacture, including its specifications, design issues, cost of production and regulatory requirements. Not knowing or understanding the desired output can give rise to quality issues, production cycle slowdown and damage to machine or mould. Therefore, you must have a clear idea of various aspects of the item output such as plastic-type, item dimension, estimated time for cycle, gate location, weight, etc.
2. Choose the Type of Machine
Injection moulding machines are of mainly three types: hydraulic, electric and hybrid which is a combination of electric and hydraulic drive.
There are several aspects to keep in mind for each machine type. For instance, using a servo pump control to save power will only be effective if you have extended cooling periods or times when the machine is not in use.
3. Determine the Necessary Clamp Tonnage
You can determine this using any of the three methods listed below:
- Machine manufacturers and injection moulders often have this knowledge. You can ask for this information from equipment providers.
- Determine clamp tonnage using computer simulation software.
- Determine the clamp tonnage yourself by measuring the variables, including cavity pressure, surface area, depth and material type.
4. Determine the Size of the Injection Unit Needed
Manufacturers typically offer two options of injection units to choose from a particular tonnage. To choose the right one, you need to calculate the shot size as an injection capacity percentage.
Following the above steps will let you determine the right machine. However, funding-related contingencies might arise as these machines are expensive and require heavy investments. In such a scenario, a Machinery Loan from Poonawalla Fincorp can be the perfect solution. It provides you with benefits like an affordable interest rate, quick loan disbursal, flexible loan tenure, option for part-payment and foreclosure and much more.
Also Read - Get Machinery Loan With Security in India
How to Apply for a Machinery Loan From Poonawalla Fincorp?
You can apply for a Machinery Loan by following these three simple steps:
- Step 1: Click on the ‘Apply Now’ button.
- Step 2: Fill in the required details on the loan application form.
- Step 3: Upload necessary documents.
On successful verification, the loan amount will be disbursed into your bank account instantly.
Also Read - Why Get Used Machinery Loans Instead of Buying New Equipment?
To conclude
There are many benefits of plastic injection moulding in the manufacturing industry. It offers cost-effectiveness, faster production cycles, design flexibility, consistent output items and the ability to create complex shapes with high precision. Additionally, it allows for the use of a wide range of materials, making it versatile for various industries. Overall, plastic injection moulding is a valuable process that contributes to efficient and reliable manufacturing processes.
We take utmost care to provide information based on internal data and reliable sources. However, this article and associated web pages provide generic information for reference purposes only. Readers must make an informed decision by reviewing the products offered and the terms and conditions. Loan disbursal is at the sole discretion of Poonawalla Fincorp.
*Terms and Conditions apply